Occupational Health, Safety and Work Environment
SMPC’s occupational health and safety management falls under the purview of Occupational Safety, Health, and Working Environment management. This management is guided by a policy established in accordance with Thai and international standards and practices. The policy adheres to the principles of occupational health, safety, and working environment management, and includes the following components:
- Ensuring personal safety of operators.
- Ensuring safety of machines and the production process.
- Meeting legal requirements to ensure a safe working environment.
- Providing healthcare for employees.
- Implementing effective pandemic management measures.
Occupational Health, Safety and Work Environment Policy
The company established the Health & Safety Board of the Committees on 14 November 1988. The Board of Committee consists of the professionals from various departments of SMPC, and representatives from the contractor company whose roles are observers. The term of committee is 2 years. At present, there are a total of 13 safety committee members and the safety committee meeting is held on a monthly basis. Their roles and responsibilities are as follows
- Prepare a policy on safety, occupational health and the working environment of the establishment and present it to the employer. The policy and goals for 2024 will continue from previous years, which is to reduce lost-time accidents to zero.
- Create guidelines for preventing and reducing accidents, danger, illness or nuisance arising from the employee’s work or job insecurity. Then it is to report to the employer.
- Report and suggest measures or ways to improve working conditions and the working environment in accordance with the law regarding work safety, to the employer for the safety of the employees, contractors and outsiders who come to perform work or come to use services in the company premise.
- Promote and support occupational safety activities in the company premise.
- Review the manual on occupational safety, health and working environment of the business establishment in order to present opinions to the employer.
- Survey work safety practices and report the results of the survey. Including statistics of dangers that occur in that business premise in safety committee meeting along with reporting to employers every quarter.
- Review a project or training plan regarding occupational safety, including projects or training plans regarding the roles and responsibilities in safety of employees, supervisors, executives, employers and personnel at all levels to present opinions to the employer.
- Set up a system so that every employee at every level has a duty to report unsafe working conditions to the employer.
- Follow up on the progress of matters presented to the employer.
- Report annual performance, including identifying problems, obstacles, and suggestions for performing the duties of the Safety Committee after one year of service to the employer in order to evaluate the safety performance of working in premises.
- Evaluate the work safety performance of the company premise.
- Perform other work safety tasks as assigned by the employer.
In 2024, there were no serious accidents that resulted in disability or death of employees and contractors working in the company’s premises. But there were still lost time accidents of employees and contractors, that do not meet the company’s goals. However, the accidents in 2024 compared to 2023 has increased by 7%. The company had guidelines to prevent repeated accidents. When accident happened, the Occupational Safety, Health and Work Environment Committee and related parties jointly investigated and analyzed the cause to find solutions and prevent recurrence, in order to achieve the goal of reducing lost time accidents to zero. The company therefore has plans and operations as follows
Performance
Targets and injury statistics for employees and contractors working on the company’s premises are as follows:
In 2022, there were no serious accidents resulting in disability or death among employees and contractors working on the company’s premises. However, there were lost time accidents involving employees and contractors, which did not meet the company’s goals. Nevertheless, there was a decreasing trend in accidents compared to 2021. The employee accident rate decreased by 17%, and the contractor accident rate decreased by 9%. The company has implemented guidelines to prevent recurring accidents. In the event of an accident, the Occupational Safety, Health, and Working Environment Committee, along with relevant parties, conducted joint investigations and root cause analyses to find solutions and prevent a recurrence, aiming to achieve the goal of zero lost time accidents.
Activities to Reduce Accidents from Work
The company supervises and improves all working areas to be safe and have a good working environment according to occupational health. The company believes that operational safety is in place when employees and operators are well aware of the dangers and risks that may occur, as well as truly understand safety measures. Company has implemented important activities as follows
- Safety knowledge training. The company has trained on the safety of working for employees at all levels, both new and existing employees, including the contractors working in the premises of the company, according to the necessity of each task and working area.
- Personal safety equipment is provided to workers which is suitable to the nature of the work. The company makes employees aware of the importance of wearing safety equipment. Supervisor level, safety officer, and professional safety officers strictly inspect to ensure that employees and contractors are wearing personal protective equipment correctly and appropriately.
- Working environment measurement. There are measurements as required by law once a year, such as measuring the concentration of chemical, air quality, sound, and heat in the working area. The results of the measurement in 2024 were found to pass the standards required by law.
- Analysis and evaluation of the security risks. The company analyze safety work to find the possibilities of any danger that may occur, and risk points that may cause danger from operations, along with finding solutions and preventing danger. There is analysis to identify hazards (JSA), and measures to prevent every activity.
- A total of 7 annual emergency drills are held, which are prevention and suppression of fire, hazardous chemical leakage, flood and wastewater overflow, radiation emergency, gas leaks and accident prevention to respond to emergencies in case of leakage, fire and explosion of industrial waste.
- Check compliance with laws regarding safety, occupational health, and working environment as follows:
– Check the unsafe condition of machinery and equipment
– Check the wearing of personal safety equipment while working.
– Check fire extinguishing equipment
– Check warning equipment / emergency notification signals
– Check ambulance / first aid equipment / first aid room
– Arrange a meeting of the Safety, Occupational Health, and Working Environment Committee at least once a month
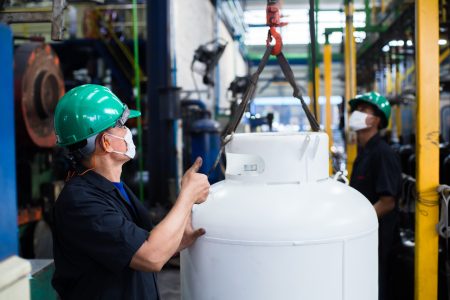
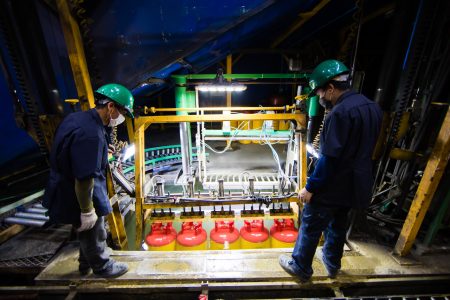